1.Low energy consumption
The energy consumed by belt conveyors is only 20% of that consumed by heavy-duty trucks.
2.Reduce waste gas and noise pollution, making it more environmentally friendly.
Using clean power resources to drive belt conveyors instead of truck transportation will significantly reduce the use of fossil fuels, while further reducing the emission of industrial waste gas and noise. There is no need to add sprinklers like in truck transportation, thus reducing water consumption. Leaving the dust and noise in the pit has greatly improved the environment of the mining area.
3.Low operating cost:
Compact crushing units, conveying units and discharging units are adopted, and an intelligent control system is employed to enhance work efficiency, reduce human resources and maintenance downtime, and lower the emissions of fossil fuels, further reducing the operating costs of mining.
4.High Security:
The crushing unit is integrated into the mine pit, reducing the use of mobile trucks. It is controlled by a remote intelligent system, which is not affected by bad weather. This greatly reduces the risks caused by human operation factors and enhances the safety of employees and the overall mining environment.
5.Complete IPCC product supply:
We can provide a full range of equipment from apron feeder, minreal sizer, belt conveyor, spreader, stroller and so on, which can all be integrated into a complete mining solution.
6.Perfect service:
We have a professional team of mine planning engineers who can formulate and implement comprehensive solutions from aspects such as engineering consultation, assessment, and design. Meanwhile, we can provide extensive after-sales support for ipcc, including parts supply, installation guidance, commissioning and operation, and mining engineering training.
Crushing Plants:
The primary crushing plant is the first step in processing ore materials, Primary crushing plant is mainly composed of apron feeder, primary mineral sizer and steel structure. According to different functions and customer demands, it can be designed as a fixed crushing plant, a semi-mobile crushing plant or a fully-mobile crushing plants.
1.Stationary Crushing Plants:
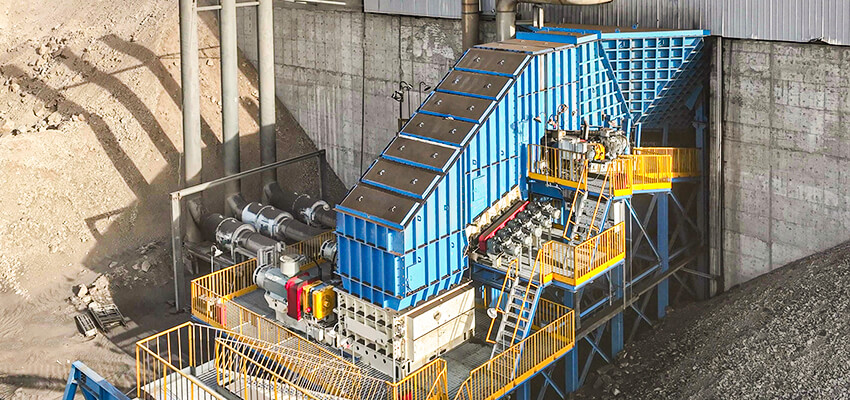
For mining sites with a relatively small depth and/or a short distance between crushing plants and factories, fixed crushing equipment is the best choice. The number of trucks can be increased or decreased to match their processing capacity.
EXCT has implemented over 70 sets of fixed crushing plants for various material types, with processing capacities ranging from 200 tons per hour to 7,500 tons per hour.
2.Semi-Mobile Crushing Plant
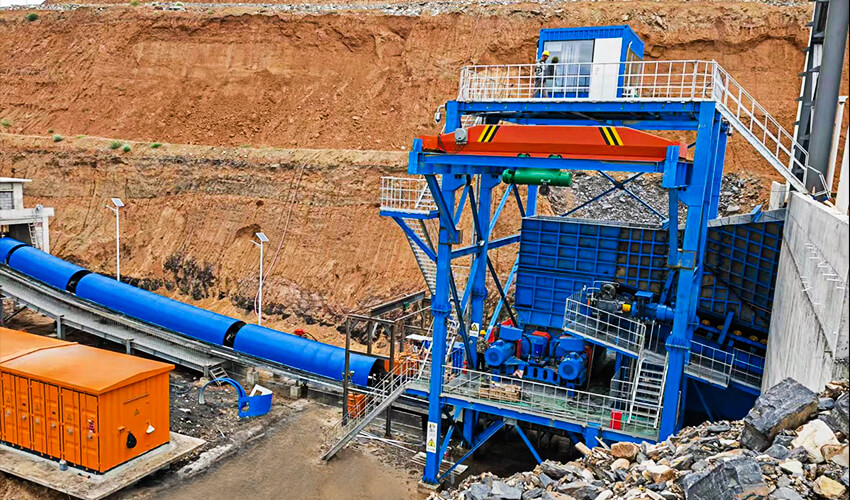
Quite a number of in pit crushing plants adopt semi-mobile crushing plants, a design that can be relocated according to occasional changes in the location of the mining site, which enhances the flexibility of mining and reduces the trucking distance after the pit moves forward, thereby reducing the use of fossil fuels and saving operating costs. This design scheme usually designs the crushing plant as a detachable steel structure and uses traction crawler vehicles to move it to the new mining site.
3.Fully-Mobile Crushing Plants
EXCT 's fully mobile crushing plants are in the form of crawler, wheel or traveling device. fully mobile crushing plants highly integrate mineral sizer and apron feeder into mobile tracked vehicles, wheeled or walking equipment to enable self-all-round movement in order to accommodate the connection between the bucket and the truck.
Conveyor System:
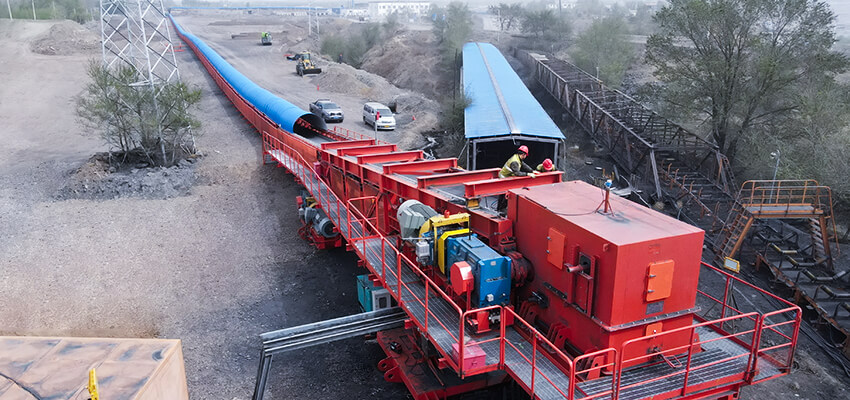
The belt conveyor system can be used in conjunction with crushing equipment to transport crushed materials to factories or stockyards. According to customer requirements, the belt conveyor can be designed in either a fixed or mobile layout. Especially in open-pit mining environments, this system can handle material transportation tasks with inclinations and curved paths. We offer an "in-pit crushing and conveying solution" that combines a crushing system with a conveying system. Our belt conveyor system is designed using self-developed professional design software and 3D dynamic simulation technology to ensure the authenticity of data feedback and the accuracy of the design plan, thereby guaranteeing the stability of the conveying system during later operation, the rationality of material flow, and the high availability of the system.
Crawler-Mounted Spreaders:
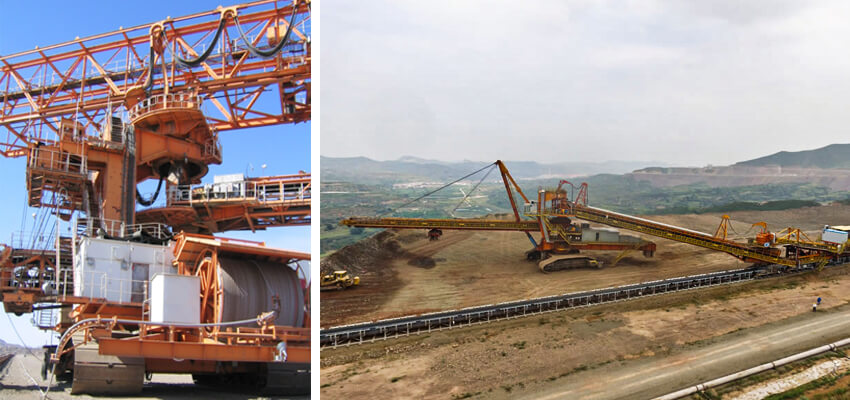
As the terminal link of the continuous mining system, the spreader undertakes the core function of material distribution. This mobile equipment receives the stripping materials or ores from the front end by connecting to self-unloading mobile conveyor platforms, unloading vehicles or mobile transfer machines and other transportation devices. Then, through an intelligent control system, it evenly spreads the materials at the designated positions in the waste dump or stacking area according to the preset parameters, ensuring the stability of waste accumulation and the efficient utilization of subsequent operation space. Our ipcc uses crawler hoists to complete the soil discharge operation.
Features:
1. Coating layer spreading process
In the surface stripping operation of open-pit mines, self-propelled spreaders are used to regulate the spatial distribution of the covering layer materials. This equipment realizes the layer-by-layer paving process through the GNSS automatic navigation system, and the deviation of the paving thickness is controlled within ±15cm. This process enhances the bearing capacity of the foundation of the waste dump to over 200kPa, increases the slope stability coefficient by 30%, reduces the secondary leveling workload by 45%, and effectively meets the environmental control indicators.
2. Leaching yard construction process
The intelligent hoisting system based on DEM three-dimensional modeling (equipped with a laser scanner) performs ore stratification operations. The layer thickness was maintained at 1.5±0.2m through PID closed-loop control (YS/T 5030-2019 specification), and the surface slope of the storage yard was controlled within the range of 5-8°. This technology stabilizes the solution permeation rate at 15-20L/(m²·min), increases the metal leaching rate to 92.5%, and through the optimization of the permeation layer structure, the drainage efficiency reaches 300m³/h, and the process reliability index (MTBF) is extended to 1500 hours.
3. Cross-pit transportation technology
The stripping material transportation operation was carried out by using a cantilevered cross-pit spreading unit (with a working radius of 60m and a rotation Angle of ±110°). This equipment realizes joint operation with the electric shovel through the CAN bus system, with a transportation efficiency of 3,500 tons per hour, saving 40% of fuel consumption compared with the traditional truck transportation mode. The technological innovation points include:
① Construct a spatial parabolic material trajectory model, with the positioning accuracy of the drop-off point being ±0.5m
② By adopting modular assembly bridging technology, the amount of temporary road engineering is reduced by 70%
③ The cantilever deflection < L/500 is controlled in real time through the strain monitoring system (GB 50017 Steel Structure Code)