At present, double-tooth
mineral sizers are widely used in the coal field in our country, mainly with four structures of tooth ring type, tooth plate type, tooth cap type and integral roll type. Tooth plate crusher is favored by customers for its advantages of convenient maintenance, flexible layout, reasonable crushing mechanism, strong adaptability, large production capacity, energy saving and low cost of parts. However, it is easy to produce manufacturing errors in the manufacturing process, and there are often problems such as the tooth plate can not be fastened by the drop or deformation of the stop box during the use of the tooth plate, and the disassembly is difficult when the tooth plate is replaced. Based on this, the author analyzed the problems existing in the fastening structure of the tooth plate, and improved it to improve the assembly accuracy of the tooth plate, make the replacement of high-strength bolt components convenient and fast, shorten the maintenance time, and enhance the stability of the product and the competitiveness of the industry.
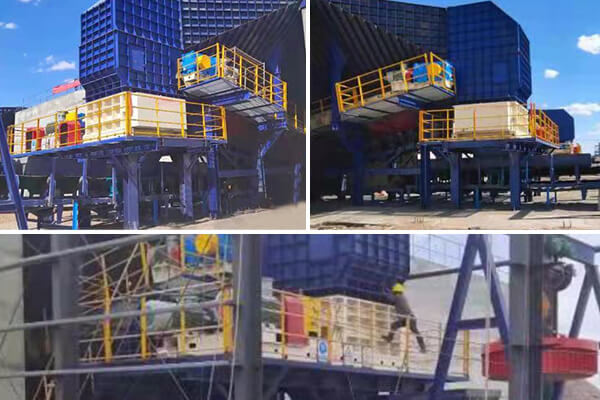
1.Mineral sizers tooth plate assembly form
1.1 Tooth plate fastening structure Tooth plate
mineral sizers are widely used in some working conditions with low crushing strength because of their convenient disassembly. The fastening structure of the tooth plate is mainly composed of a stop box, T-bolt, washer, nut and other parts.
The assembly process is as follows: (1) Install a plurality of crushing roller seats on the shaft, and lock the roller seats with round nuts or clasp rings; (2) The crushing roller seat generally contains a number of faces, each face has a long groove, according to the size requirements of the drawing in the groove welding stop box, surfacing welding stop box and groove between the cavity between the roll seat, welding stop box; (3) Install the tooth plate so that the hole of the tooth plate corresponds to the hole of the stop box; (4) Load T-bolts, washers and nuts: (5) Repeat the above assembly process on multiple surfaces of the crushing roller to complete the assembly of the tooth plate of the tooth roller.
1.2 Tooth plate fastening structure defect tooth plate assembly process is simple and convenient, favored by customer groups.
However, this structure also has its own defects: (1) the stop box is a cast part, and the casting defects on the surface may affect the assembly of the T-bolt and the welding of the stop box. It is necessary to try to install the T-bolt before use, and check whether the bottom surface of the stop box has convex points. (2) During the welding process, the stop box will be deformed, and the opening hole on the stop box may jam the T-bolt. After the stop groove is welded to the roller seat, the tolerance of the hole inside the roller seat changes, and the shaft can not be reused during the overhaul of the tooth roller. (3) The thread of the T-bolt extending out of the nut is exposed, which is directly in contact with the working environment, and the thread will rust or damage, affecting the disassembly of the tooth plate. (4) The two sides of the opening hole on the stop box are directly in contact with the working environment, and the coal ash fills the box body, affecting the disassembly of the T-bolt.
2 On-site maintenance
The tooth plate is the main wear part of mineral sizers [4]. When working, it comes into direct contact with the material and is subjected to extrusion pressure and abrasive wear caused by the material. The main failure forms are deformation, fracture and wear of the tooth crown. The increasing wear degree of the tooth plate will increase the discharge particle size of the crusher, and the tooth plate needs to be replaced to ensure the performance of the crusher. Due to the connection characteristics of the tooth plate and the crushing roller seat, the material blocked on the connection bolt of the tooth plate should be cleaned first, and then the T-bolt should be removed. After removing the worn tooth plate, the new tooth plate should be replaced and the T-bolt should be tightened. Because the crusher in operation for a long time, the T-bolt hole on the tooth plate is blocked by relatively viscous materials, must be cleaned to remove the T-bolt on the tooth plate, labor intensity, poor working environment, small space, resulting in the replacement of the crusher tooth plate than expected complex difficult.
(1) The joint of T-bolt and nut and the exposed thread cannot be removed normally due to rust or damage, and the nut must be cut by riveting and cutting. The small slot on the tooth plate increases the difficulty of rivet cutting.
(2) The coal ash compaction in the stop box is not easy to remove, and the T-bolt head is stuck, increasing the difficulty of disassembly.
(3) Due to the long-term operation of the crusher, the tooth plate drives the T-bolt to pull the hole on the stop box, which will cause the T-bolt to be unable to tighten the tooth plate. Deformation hours can be simple repair, but the working strength and reliability will decline: when the pulling is serious, the stop box can not be restored by on-site repair, need to overhaul the crushing roller or replace the crushing tooth roller, affecting the normal production operation on the site.
3 Improvement Plan
Mineral sizers Fastening quality directly affects the stability of the equipment, upgrade and reform the fastening structure of the tooth plate, reduce the workload of riveting and welding, improve the precision of the tooth plate assembly, make the replacement of high-strength bolt components convenient and fast, shorten the maintenance time, enhance product stability and competitiveness in the industry.
3.1 Improved tooth plate and roller base connection form the key is generally made of 45 steel, is used to connect the shaft parts and the role of circumferential fixation, in order to achieve the transmission of torque example of a mechanical part, the key connection is through the key to achieve the shaft and the shaft parts between the circumferential fixation to transfer movement and torque. As a standard part, the key plays an irreplaceable role in the manufacturing, installation and processing process. Key selection includes type selection and size selection. When selecting the type of key connection, it is generally necessary to consider the size of the transfer torque, whether the parts on the shaft move along the axis and the size of the moving distance, the neutral requirements and the position of the key on the shaft, and analyze the selection combined with the characteristics of various key connections. The section size of the key (key width b and key height h) is selected according to the diameter d of the shaft from the relevant standard; The length of the key L can be determined according to the length of the hub, preferably the key length is equal to or slightly shorter than the width of the hub. In the improvement of the assembly structure of the tooth plate, the flat key connection is adopted, and the flat key connection makes the tooth plate and the roller seat connect into one. The two sides of the flat key are the working face, and the flat key connection is to transfer the torque by pressing the side of the key and the keyway, and there is a gap between the tooth plate key and the bottom of the roll seat groove. The strength calculation of the key connection varies slightly with the difference of the key connection, but the calculation method and the checking principle are the same, taking the flat key connection as an example, the strength of the key connection is checked and calculated. When the flat key connection transmits torque, the stress of each part in the connection is as follows. For ordinary flat key connections (static connections) that use common material combinations and select standard sizes, the main form of failure is that the working face is crushed, and the key is generally not cut unless there is serious overload. Therefore, the strength check calculation is usually only based on the extrusion stress on the working surface. For the guide flat key, the main failure form is excessive wear of the working surface. Therefore, the conditional strength check is usually calculated according to the pressure on the work surface.