With the rapid development of coal processing technology, coal processing equipment is constantly introduced. The main crushing equipment in open-pit crushing station, main transfer place of mine, upstream of coal chaser, wellhead preparation workshop, crushing workshop of coal preparation plant and other scenes has been replaced by jaw crusher and hammer crusher, etc., and replaced by toothed roller
mineral sizers with larger processing capacity and higher efficiency. In particular, the double-toothed roller mineral sizers, because of its simple structure, small footprint, easy connection of the feed mouth, etc., has a wider application in the market and a better development prospect. With the continuous introduction of mineral sizers, the reliability requirements of crushing teeth are becoming more and more stringent. In addition to the tooth shape meeting the parameter requirements, the basic performance of crushing teeth should also meet the use expectations. Especially in the process of heat treatment, there are problems such as insufficient hardenability, insufficient hardenability, frequent quenching cracks, and insufficient remedial measures for casting defects, which is not conducive to the large-scale development of products.
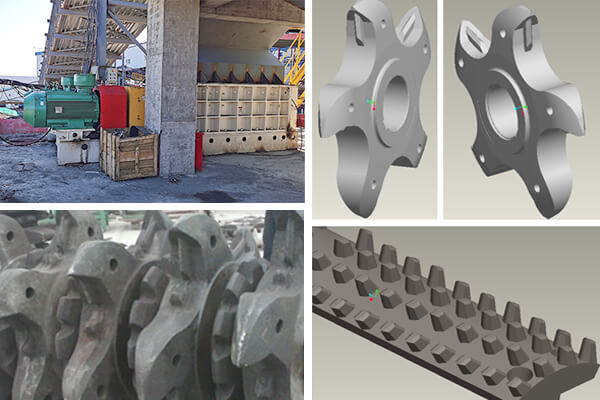
In the production practice, it is found that the raw coal in the crusher mainly comes from No. 3 coal seam and No. 5 coal seam, the coal occurrence conditions are complex, and the coal quality is poor. The pseudo-top of coal seam is carbonaceous mudstone, while the direct top is mainly sandy mudstone. The top layer of coal has poor stability and is easy to fall: the old top is sandy conglomerate, coarse sandstone, medium and fine sandstone, and the sandstone is tightly consolidated: the bottom lithology is mainly composed of siltstone and kaolinaceous mudstone. SSC700mineral sizers The gangue content in the feed exceeds 50% and contains 5% supergranular materials, which are all gangue, even gangue larger than 500 m. Crusher teeth wear is serious, the phenomenon of broken teeth frequently occurs, crusher crushing performance and crushing efficiency drop straight line, large gangue can not be broken, repeatedly turned over and rolled over the tooth roller again aggravate the wear degree of teeth, part of large gangue rolled into the crushing chamber dead Angle, stuck between the tooth ring and the crushing chamber, causing continuous wear to the edge tooth ring, and even grinding it flat. Under the impact of a large number of gangue, the round nut of the locking gear ring appears to be welded and loosened, the gap of the gear ring appears, the tooth roller shaft and teeth are broken, and the serious consequences of equipment damage and shutdown of the production site are caused. Through research and analysis, it is believed that the reasons for the poor crushing effect of
mineral sizers mainly include three aspects:
(1) The raw coal is poor in quality, and the gangue content far exceeds the design requirements of the crusher, and most of them are hard rock ore such as Kaolin rock, which requires high hardness and wear resistance of the crushing tooth material: the wear of the roller is larger, which will lead to the fracture of the tooth ring and tooth head. The fracture tooth section shows that the fracture surface casting grain is coarse and there are obvious casting defects.
(2) The design of crushing teeth is unreasonable, and the crushing of materials is mainly squeezed. In the crushing chamber, the space of material passing through is limited, and the high hardness material produces a large alternating load on the crushing teeth, which is easy to cause fatigue fracture of the crushing teeth.
(3) The locking structure of the tooth roller ring is poor, which is more suitable for the crushing environment where the coal quality is good and the impact of the material on the tooth roller is small, and it is easy to malfunction when dealing with high hardness materials, causing fatal damage to the equipment. Comprehensive analysis, due to mineral sizers casting material is poor, tooth profile design is not reasonable, tooth roller tooth ring lock structure stability is poor, can not meet the site crushing requirements. After repeated demonstration, the coal preparation plant decided to replace the crushing gear roller assembly according to the actual working conditions, optimize the casting material of the tooth ring, redesign the tooth profile, and upgrade the locking structure of the tooth ring to ensure the reliable operation of the crusher.
After increasing the content of C and S1 in mineral sizers, adjusting the casting temperature, quenching temperature, holding process and tempering temperature, through data analysis, the hardness and wear resistance of the fracture ring are better than those of the original fracture ring, and a method to preliminarily improve its performance is found.
(1) The material performance enhancement experimental data show that the carbide is more evenly distributed in the material, the thickness of the decarburization layer of the casting before quenching is reduced, and the overall hardness and wear resistance of the crushing teeth are significantly improved:
(2) Increase in manufacturing cost, increase in casting risk Increase in alloy content increase in material cost, increase in heat treatment holding time increase in power consumption cost, increase in toughness while material hardness increases, increase in finishing cost, increase in C content increase the hot cracking tendency of castings, residual stress after quenching increases the probability of fine crack expansion in castings, which is not conducive to maintaining stability. Foundry indirect cost increase:
(3) There is still room for adjustment of element ratio and heat treatment process The
mineral sizers fracture ring sample that meets the performance requirements was obtained by material fine-tuning and heat treatment process change. Local cracks also appeared in the actual casting, which proves that there is still room for adjustment of element ratio and heat treatment process. Maintain stable casting production.