1.Increase the guiding mechanism to prevent the belt from running off. In the production practice, the belt edge of the traditional
corrugated sidewall belt conveyor has a long-term friction with the turning belt pulley or the vertical roller and the base belt, causing the belt to wear and break and the base belt tear after a short working time. Phenomenon, reducing the service life of the corrugated sidewall belt. The corrugated sidewall belt is expensive, so fundamentally solving this problem can greatly reduce the cost for the user to use the machine, reduce the time taken to repair the belt rupture or replace the belt, and improve production efficiency. The main reason for the above phenomenon is that the traditional sidewall conveyor frame adopts a welded structure, the installation accuracy is difficult to meet the design requirements, and because there are ribs and partitions on the belt, the aligning roller cannot be installed like a flat belt conveyor. The belt runs too far.
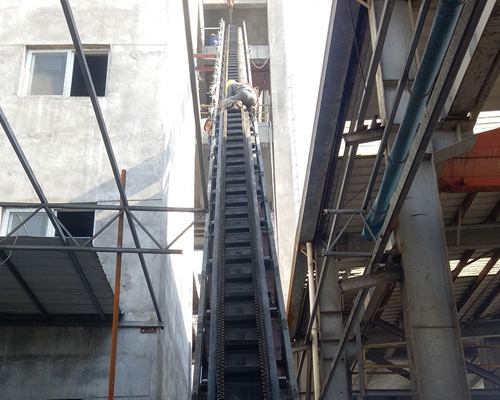
2.Optimize the fuselage structure and manufacturing process. The main structure of the conveyor is generally a welded piece of channel steel, and the overall quality of the
corrugated sidewall belt conveyor is very large. The degree depends on the technical level and installation conditions of the on-site installation workers. In practice, because the installation accuracy does not meet the design requirements, the belt deviation phenomenon occurs, causing the belt to wear sharply or the equipment cannot operate normally. In addition, due to the overall structure of the channel steel structure poor rigidity, special truss and auxiliary support frame are needed to improve the rigidity of the whole machine, resulting in complicated structure, long installation period and high cost. Therefore, it is necessary to improve the structure of the fuselage. After the improvement, the whole fuselage is a web-shaped structure with the entire steel plate bent, and the bolting is used instead of the welding to ensure the rigidity of the whole frame, and the truss and the auxiliary support frame are not required; the mounting holes on the right wall panel are adopted. The combination drilling process is used to ensure the installation accuracy; the support square steel adopts post-weld milling and combined drilling processing to eliminate the welding deformation and achieve the best parallelism between the rollers, ensuring that the belt does not run off and improve the belt life; The connecting plates are connected by bolts between the racks, which not only avoids welding deformation, but also has quick installation on site, and has low technical requirements for the installation workers. The biggest advantage of the equipment after the improvement of the frame structure is that the machine has a simple structure, good rigidity, high manufacturing and installation precision, and is convenient for belt installation, replacement and equipment maintenance.
3.Make the vibration cleaner steerable. When the material being conveyed is not adhered, the flapping roller can be manipulated to raise its center without coming into contact with the sidewall belt. At this time, since the tapping roller is no longer rotated, the corrugated sidewall belt is no longer vibrated.
The
corrugated sidewall belt conveyor has a large conveying inclination angle of up to 90°, which saves floor space, saves equipment investment and civil construction costs, and is ideal for large dip angle conveying and vertical lifting. The structure is simple, and all the main components can be used in common with the belt conveyor, which is convenient for use and maintenance. Reliable operation. There is no slipping or falling down that often occurs with bucket elevators, and its reliability is almost equivalent to that of a universal belt conveyor.