The crushing & screening system of HuaYin Aluminium Mine Plant using the screening process of “pre-screening”. This means that the ore is conveyed by the belt conveyor into the
inclined screen for pre-screening, then the ore returns crushing equipmen to crushing the material, after crushing, the ore into the inclined screen again for screening. During the productive process, they using the 2 sets YKR3060 inclined screen, the installation angle is 15°, the screen hole is 38mm*20mm, the size range of feeding particle is ≤85 mm, the ore size less than 15 mm will into the storeage, while the size greater than 15mm return to the crushing equipment.
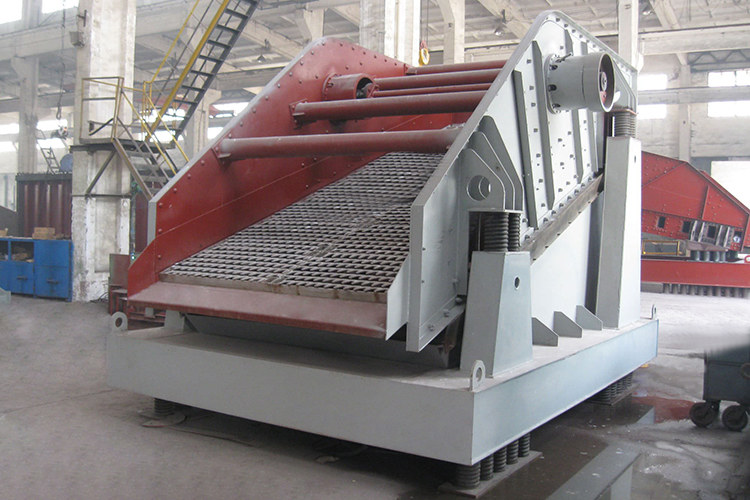
In the operating of the first year, the using effect of inclined screen is not ideal, it became a problem in the productive process. Leading to the crushing capacity is only 350t/h, far below client’s requirement. At the same time, the mesh of inclined screen is easy to breakage, the service life of each screen is about 150,000h, while other equipment faults often occur, such as flexible plate fracture, spring damage, box cracking, girder fracture, etc. As a result, the monthly downtime for maintenance exceeds 8 days, which not only affects the normal production requirements, but also increases the maintenance cost of the equipment. The low productivity of the screen and the high failure rate of the equipment seriously affect the normal crushing production.
Analysising the main reasons
According to the operation in site, the main reasons leading to the unsatisfactory use effect of the inclined screen are as follows:
Uneven force on screen surface
Uneven of material feeding. A herringbone discharge hopper be installed under the
inclined screen. Because belt deviation, material stacked on the hopper and other faults, the material splitting is uneven. As a result, one side of the screen is seriously overloaded, while the other side of the screen is almost empty, so it ifter causes uneven wear and damage of the screen faster.
Screen surface stress and Uneven distribution of materials. The distance between the funnel and the feeding end of the inclined screen is too high, reaching 400mm. When the ore enters the inclined screen through the funnel, the impact force on the feeding place is too large, which causes the girder fracture and box cracking at the feeding place. After ore enters the inclined screen feeding end, the distribution is not even, the ore always runs to one side, only half of the screen plays the role of screening, resulting in serious ore deposit at one side and low screening efficiency.
The material residence time on the screen is too long
The ore moves slowly on the screen, and there is too much ore on the screen, up to 200 mm thick. The material movement speed on the screen is about 0.2m/s. The ore movement speed is too slow, resulting in too much ore deposit on the screen surface. So, the inclined screen is always in the state of overload operation, resulting in rapid damage to the screen, flexible coupling tear, spring damage, girder fracture, box cracking and a series of faults.
Solutions
Increasing distributor. According to the uneven material distribution in the hopper, a distributor is added at the feeding port of the belt. The distributor can move around according to the deviation of the belt to evenly divide the ore into the two sides of the funnel and enter the inclined screen to make the two sides of the feed relatively balanced and solve the problem of uneven material feeding.
Reducing theheight difference to adjust the position of hopper. By reducing the funnel and inclined screen into the material discharging end the elevation difference, the original design of 400 mm to 250 mm, the ore very smoothly into the
inclined screen, greatly reduce the ore of inclined screen impact, make force is relatively balanced, inclined screen have effect to solve the housing problem such as craze, longitudinal beam fracture. At the same time, in order to solve the uneven distribution of ore at the feeding port, the feeding funnel position is widened at the feeding port, so that the material is evenly distributed on the whole screen surface and the screening efficiency is greatly improved.
Increasing the inclination angle of screen to improve the move speed of ore. The slow movement of ore on the screen leads to thick deposit and serious ore pressure. The main factors affecting the moving speed are the amplitude of the inclined screen and the slope of the screen. Under the condition of the same feed quantity, the slope of the inclined vibrating screen is increased, the running speed of the ore is raised, and the time of ore staying on the screen is reduced. There is no ore accumulation or ore pressure on the screen surface, and the material can be loose, stratified and screened on the screen surface, and the processing capacity is greatly increased. At the same time, the failure rate of the inclined screen and the loss rate of the parts are also greatly reduced.