Generally speaking, the screening process of
trommel screen is a probability event, the particles appear on the screen for many times, and every time when it appeared on screen, there is a known probability is a known probability of particle size of particles through the sieve pore, thus negatively impact probability of particles through the sieve pore factors also influence the reliability of drum sieve sieve, there are many factors can affect the probability of particles through the sieve pore.
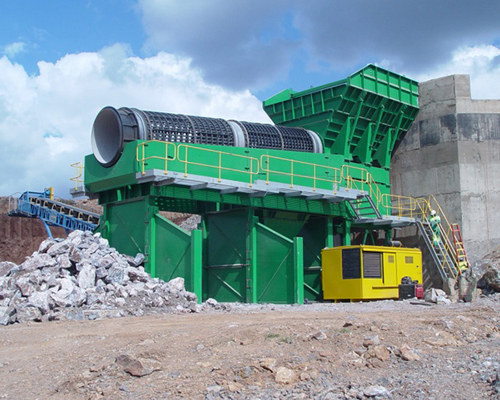
1.Granularity. When the particle size is close to the size of the sieve hole, the efficiency of the drum sieve decreases obviously. The screening efficiency of the main drum decreases obviously with the increase of the proportion of particles near the sieve hole. The role of near-sifter particles is multifaceted, as they tend to limit or block the sifter, reducing the effective drum screen area of the sieve. This is the process in which the sieve often appears in the closed-circuit crushing process. In the closed-circuit process, the material close to the sieve hole gradually increases, which reduces the efficiency of the drum screen gradually.
2. Feeding speed. The analysis principle of separation degree of
trommel screen is that it can achieve almost complete separation by using lower feeding speed and longer drum screen. In the practice of drum screening, considering the economic cost, it is required to adopt higher feeding speed and reduce the residence time of materials on the screen surface.At a higher feeding rate, a thick bed is formed on the screen, and fine particles must pass through the thick layer to have a chance to pass through the screen further.The final result is to reduce the efficiency of drum screen.For any separation operation, high yield and high efficiency are often contradictory requirements. In order to get the best results, the above two indexes must be considered comprehensively.
3. Sieve inclination Angle. If the particles approach the sieve hole with a small inclination Angle, making the sieve "look" is the effective aperture of the end, and the particles near the sieve hole can hardly pass through. The inclination Angle of sieve surface affects the Angle of particles entering the sieve hole. Some sieves use this function to separate materials finer than the sieves.The sieve Angle also affects the velocity of particles moving along the sieve surface, the residence time on the sieve surface and the probability of particles passing through the sieve surface.
4. Particle shape.Most of the material particles processed on the screen are non-spherical.When the spherical particles pass through with equal probability in all directions, the irregular near-sieve particles must pass through the sieve in a certain direction.Elongated and platy particles have a smaller cross-sectional area in one direction and a larger cross-sectional area in other directions. Therefore, the highly irregular shape of the grain drum screen screening efficiency is reduced.
5. Effective screening area. The probability of screening through the
trommel screen is proportional to the percentage of effective drum screen screen area. Effective screening area refers to the screen area and screen surface area ratio. The smaller the screen surface occupied by the screen material, the higher the probability of particles entering the screen hole. Effective screen area decreases with the size of the sieve hole. Therefore, in order to increase the effective area of the sieve diameter of the small hole, it is necessary to use the thin and brittle sieve wire, but the sieve mesh is easy to wear and the treatment capacity is low. This is also the reason why fine - grained materials are classified by classifier instead of screen.
6. Vibration. In order to remove the material from the screen, the screen should be vibrating, which makes the material fall back and move along the screen again. Appropriate vibration can also cause layering of the feed, which causes fine particles to pass through the material layer and reach the screen surface downward, thereby raising the large particles to the top. Layering can increase the pass rate of the middle part of the sieve.