A Feeder Breaker is a specialized piece of equipment designed to transfer mined materials from transportation equipment to unloading points. It not only provides robust storage capacity but also significantly reduces material handling cycle times.
In practical applications, the Feeder Breaker is particularly suitable for underground and open-pit mining of brittle minerals such as coal, lignite, salt, and gypsum. It also plays a crucial role in the processing of coke in delayed coking units. It can receive large pieces of fragile mineral raw materials and crush them into products with a one-dimensional size ranging from 6 inches to 12 inches (150 mm to 300 mm), with a processing rate of up to 6,000 tons per hour (5,400 metric tons). Additionally, depending on the feeding method, the Feeder Breaker's design storage capacity can reach two to three times the load capacity of transport vehicles, enabling multiple transport vehicles to operate in a manner at optimal efficiency.
Working Principle of the Feeder Breaker
Feeding Principle: Feeder breakers typically use chain conveyor belts or similar feeding devices. The drive sprocket moves the chain horizontally, with scrapers or chain links dragging the material uniformly into the crushing zone from the feed opening, relying on thrust and gravity for continuous conveying.
Crushing Principle: Common crushing methods include tooth roller crushing and hammer crushing. In tooth roller crushing, rotating tooth rollers crush materials through impact, compression, and tension, utilizing the interlocking teeth to break down the material. In hammer crushing, high-speed hammer heads strike the material, causing it to repeatedly collide and fracture between the hammer heads and chamber walls until the desired particle size is achieved.
Control principle: The automatic control system monitors material flow, particle size, and equipment status via sensors, transmits data to the PLC controller, and automatically adjusts feeding speed and crushing force. In case of a fault, it immediately alerts and stops the machine. Some equipment supports remote control, enhancing safety and convenience.
What are the main components of a feeder breaker
Frame
A robust frame is the foundation for the long-term stable operation of the Feeder Breaker. All Feeder Breakers are constructed from heavy-duty steel plates welded together, reinforced with extensive structural supports to withstand years of high-intensity operation and severe impact loads. The top of the frame, both sides of the chain, and areas in contact with the material are covered with replaceable wear-resistant liners. These liners are installed using either welded or bolted fasteners depending on replacement frequency, effectively extending the equipment's service life.
Sprockets and Shafts
The head shaft and tail shaft are designed for complete disassembly through maintenance panels, facilitating maintenance and replacement. The shaft bodies are made of alloy steel that has undergone quenching, tempering, and stress-relief treatment, and are paired with bushings for tension adjustment. Sprockets are made of solid flame-hardened steel or feature a split-design, offering more maintenance options. Both the head shaft and tail shaft areas are equipped with split bushings to prevent excessive shaft wear. At the points where the shaft passes through the frame openings, grease seals are used to prevent leakage, and under-speed sensors are installed to protect the shaft from damage caused by high torque.
Chain Conveyor
Feeder Breaker offers two chain conveyor configurations: single-drag and double-drag. The choice of configuration primarily depends on the processing capacity required by the production process. The double-drag system is more suitable for scenarios with higher processing capacity requirements or when the Feeder Breaker is installed below a large hopper. Solid steel scrapers are connected to the engineering-grade chain via various pin connection methods, ensuring stable material conveyance.
Conveyor Drive System
Chain conveyors are available with either hydraulic or electromechanical drive systems. Hydraulic drives offer flexible speed control and provide cushioning effects to effectively handle impact loads; electromechanical drives feature torque control couplings between the motor and reducer, protecting the coupling and related components when the conveyor becomes blocked or jammed. Additionally, the electromechanical drive is equipped with an automatic reverse system. When a blockage occurs, the conveyor can automatically reverse to clear the blockage or retrieve foreign objects until the blockage is resolved or the pre-set retry count is reached.
Drive Device
The drive device is divided into two modules: crushing drive and conveying drive.
The crushing drive device is composed of a motor-coupler-reducer. The coupler is mainly used to connect the power source and the working machine, and transmits torque through the change of liquid momentum. This power transmission method can not only ensure the normal operation of the crusher, but also reduce the impact force at startup and protect the motor and crusher from overload damage.
The conveying drive device is composed of a motor-coupling-reducer. The main function of the coupling is to connect the transmission device and the conveyor to ensure that the two can rotate together and transmit power and torque.
Crushing Rollers
The design of the crushing rollers is intended to cause material fracture and breakage rather than simple compression crushing. Since the rotation direction of the crushing rollers aligns with the material flow direction, the material undergoes simultaneous force from multiple crushing teeth as it passes through the rollers, causing it to fracture along its natural fracture planes. The crushing rollers use replaceable hard alloy cutting heads, secured with retaining rings or spacer rings, and arranged in a spiral pattern. Depending on the application, the arrangement of the cutting heads and the spacing between the discs can be adjusted. Additionally, the crushing rollers are equipped with flywheels to increase crushing power, effectively crushing high-hardness materials and reducing the risk of equipment downtime in complex operating conditions.
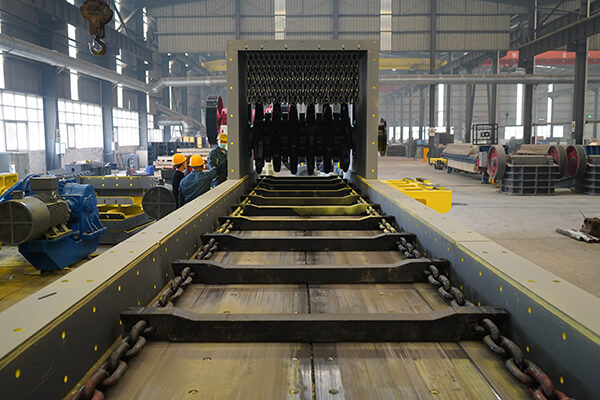
Feeder Breaker Features and Advantages
Core Design Features
- Tungsten carbide cutting heads: Utilizing tungsten carbide cutting heads offers advantages such as low cost, easy replacement, and high wear resistance, significantly reducing equipment maintenance costs and downtime.
- Automatic chain tensioning: The automatic chain tensioning system maintains chain tension in real-time, ensuring stable conveyor operation and minimizing faults caused by chain loosening.
- Optimized Crusher Head Design: The precisely designed crusher head achieves efficient crushing while reducing energy consumption and enhancing overall equipment performance.
- Durable Structural Components: The equipment features bolt-fixed chain tensioning devices, welded high-strength steel platform plates, and bolt-connected side plates and skirt plates, ensuring robust and durable structural integrity.
Significant performance advantages
Compared to traditional feeder and screen combinations, the Feeder Breaker offers multiple significant advantages:
- Energy-efficient and cost-effective: The Feeder Breaker employs an advanced power transmission system, significantly reducing energy consumption during operation. Compared to traditional equipment, its energy utilization efficiency is greatly improved, effectively reducing electricity costs in the production process and delivering significant economic benefits for business operations.
- Expert in handling oversized materials: When dealing with oversized rocks, the Feeder Breaker's innovatively designed reverse discharge rear door mechanism can quickly and safely discharge materials exceeding the processing range. In contrast, traditional feeders often get stuck with oversized materials in the head chute, not only affecting production efficiency but also incurring high costs for subsequent cleanup work.
- Space Optimization Master: With the same processing capacity, the Feeder Breaker features a compact structural design, significantly reducing equipment length and floor space. This spatial advantage not only effectively saves production site resources but also provides greater flexibility for factory layout planning.
- Cost-Effective Choice: From equipment procurement to infrastructure construction, the Feeder Breaker's overall investment costs are lower than those of traditional chain feeder and screening machine combinations. Its outstanding performance and cost-effectiveness make it the top choice for enterprises seeking high-value-for-money material handling equipment.
Application Scenarios of the Feeder Breaker
Coal Mining
In the coal mining sector, the Feeder Breaker is a critical component in the coal extraction and processing chain. Coal extracted from coal seams typically contains large coal chunks, making direct transportation and processing challenging. The Feeder Breaker is deployed at the coal mining face or in the initial processing stage to crush large coal chunks into suitable sizes, facilitating smooth transportation on belt conveyors. This effectively reduces the risk of damage to the belt caused by oversized materials, ensuring efficient coal mining and transportation.
Shale Mining
In recent years, shale has gained significant attention as an important raw material for extracting oil and natural gas through hydraulic fracturing. Shale has a dense texture and must be crushed into smaller particles after extraction to facilitate subsequent grinding and milling operations. The Feeder Breaker, equipped with hard alloy cutting heads and a robust structure, effectively handles the unique texture and hardness of shale, withstanding wear during the extraction process. By crushing shale into smaller particles, the surface area of the shale is increased, significantly enhancing the efficiency of subsequent oil and natural gas extraction processes.
Gypsum Mining
Gypsum is widely used in the production of cement, gypsum boards, and fertilizers. During gypsum mining, the extracted gypsum often contains impurities and has large particles. The Feeder Breaker can crush gypsum into smaller particles, facilitating the separation of useful components from impurities, making it a critical pre-processing step for improving gypsum product quality. For example, in a gypsum processing plant, the Feeder Breaker can process up to 300 tons of raw gypsum daily, providing a robust foundation for producing high-quality gypsum board that meets industry standards.
Limestone Mining
Limestone is a crucial raw material for cement production as well as the production of lime and other construction materials. In limestone mines, the Feeder Breaker is used to crush large limestone blocks into sizes suitable for subsequent crushers and mills. Its powerful crushing capability not only improves the efficiency of subsequent processing steps but also ensures the stability of final product quality. In large cement manufacturing plants, the efficient operation of the Feeder Breaker meets the high demand for limestone in cement production, making a significant contribution to enhancing the overall production efficiency of the plant.
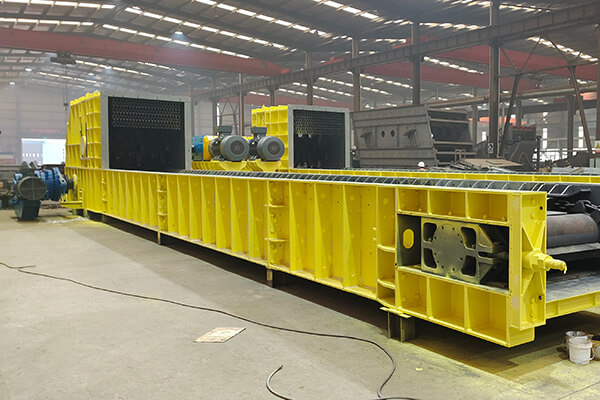
How to Select the Appropriate Feeder Breaker
- Material Characteristics: Consider material hardness, type, and moisture content. For hard materials like ore, choose crushers made of wear-resistant materials such as high-manganese steel; brittle materials are suitable for impact crushers; and for sticky or high-moisture materials, select equipment with anti-blocking designs.
- Production Requirements: Clearly define the hourly processing capacity and output particle size requirements. For high-capacity production lines, choose high-power, high-speed equipment; for fine crushing, choose impact or cone crushers; for coarse crushing, jaw or hammer crushers can be used.
- Equipment Performance: Different types of crushers are suitable for different applications. Jaw crushers are suitable for coarse crushing, hammer crushers have a high crushing ratio, impact crushers produce uniform output, and cone crushers have good sealing performance. Additionally, consider the type and adjustability of the feeding system, as well as the material of wear-prone components and ease of maintenance.
- Energy Efficiency and Environmental Protection: Select high-efficiency motors to reduce energy consumption. Install sealed covers and dust collection equipment to control dust emissions; use soundproofing materials and low-noise motors to minimize noise pollution and comply with environmental standards.
- Manufacturer Services: Prioritize well-known industry brands and review their successful case studies under similar operating conditions. Manufacturers must provide timely after-sales service and adequate spare parts supply to ensure normal equipment operation.
- Cost Considerations: Compare the comprehensive costs of equipment procurement, installation, energy consumption, and maintenance to select a cost-effective solution. Equipment with automated features such as remote monitoring may have higher initial investment costs but can reduce long-term labor and maintenance costs.
How to Maintain the Feeder Breaker for Optimal Performance
Timely Inspection and Replacement of Worn Parts
Regular inspection of the Feeder Breaker's wear-prone components is a critical aspect of equipment maintenance. Once severe wear is detected, components should be replaced promptly, ensuring the use of parts compatible with the original equipment to maintain normal operation and stable performance.
Optimize feeding methods
Properly arrange the feeding process to avoid large pieces of material or debris directly entering the crushing chamber. This effectively reduces equipment impact and wear, extends equipment lifespan, and ensures continuous production.
Enhancing the Performance of Wear-Resistant Materials
For the wear-prone areas of the equipment, methods such as overlay welding with wear-resistant materials can be used to enhance their wear resistance. By improving the wear resistance of critical areas, the maintenance frequency and costs of the equipment can be reduced.
Regular Lubrication and Maintenance
Ensuring that all lubrication points of the Feeder Breaker are adequately lubricated is key to reducing component wear. Use appropriate lubricating oil and replace it according to the specified schedule to maintain good lubrication of the equipment, reduce operational resistance, and improve equipment efficiency.
Strengthen daily maintenance management
Develop and strictly enforce a maintenance plan for the equipment, conducting regular comprehensive inspections, cleaning, tightening, and lubrication of the Feeder Breaker. Through meticulous daily maintenance, potential issues can be identified and addressed promptly, ensuring the equipment remains in optimal operating condition.
Standardize operator training
Provide professional training for equipment operators to ensure they strictly follow operating procedures, preventing accelerated wear or malfunctions caused by improper operation. Skilled and standardized operation can effectively extend equipment lifespan and enhance production safety.
Enhance Monitoring and Record-Keeping
Utilize condition monitoring and fault diagnosis technologies to monitor the Feeder Breaker's operational status in real-time and record key parameters in detail. By analyzing the data, abnormal conditions during equipment operation can be promptly identified, and appropriate measures taken to prevent major failures.
Conclusion
As an indispensable key piece of equipment in the mining and material handling industries, the Feeder Breaker plays a crucial role in various applications due to its unique design, efficient operating principles, and significant performance advantages.
Whether from the perspective of equipment selection, daily use, or maintenance and upkeep, gaining a thorough understanding of Feeder Breaker-related knowledge helps users maximize equipment performance, improve production efficiency, and reduce operational costs.