As the core component of air supported belt conveyor, the quality of the plenum chamber directly affects the whole air cushion machine performance. In the case of the industry still taking manual and semi-automatic production lines as the mainstream production mode. As a domestic professional air supported belt conveyor manufacturers, EXCT has designed and imported a international advanced technology to carry out the first domestic professional plenum chamber automatic production line (including support and crosssbeam welding), to ensure the product quality and production capacity of plenum chamber.
1. Takt time : the takt time is within 12 minutes, and the production capacity is 60 plenum chambers per day.
2. The blanking and punching molded by laser at once: the blanking of main plate and the punching of the material carrying pan are all completed one- time by two large power laser cutting machine, one is 3000W and the other is 1000W(no longer use plasma cutter), to ensure the high precision and reduce the deformation. The size of the material carrying pan of the B1800 plenum chamber is 3000 mmx2200mm, the air pocket and the pan can be one-time completed. What’s more, the position accuracy between the overall shape of the components and the connecting hole is less than 0.5 mm, so as to ensure the links of each plenum chamber unity and standard interchangeability, improving the air supported belt conveyor installation accuracy and efficiency.
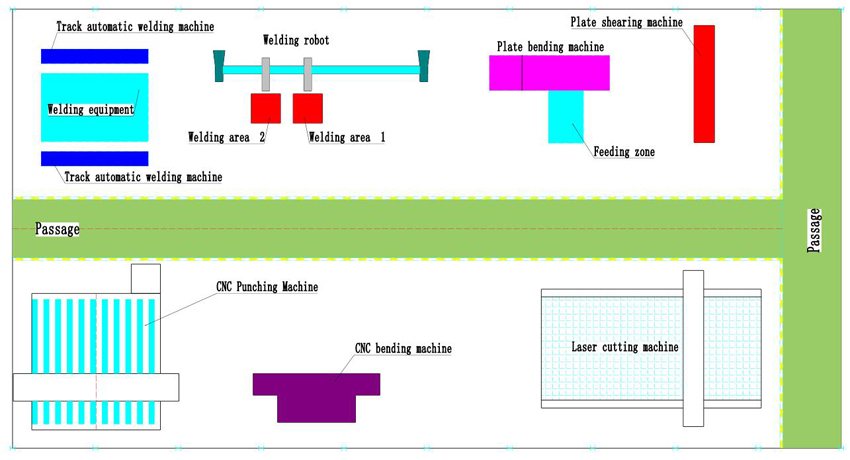
3. No deformation operation: CNC 300 ton bending machine is equipped with automatic sucker robot to grab the plate, so as to ensure the bending precision of complex shape and the transshipment process of light plate without deformation.
4. The first CNC Dual-Motion(double drive roller) four-roll plate bending machine application: the accuracy of the arc surface of the pan is directly affect the precision of plenum chamber and overall power, adopt the first CNC Dual-Motion(double drive roller) four-roll plate bending machine in the industry to eliminate the difficulty in controlling the length of arc section and the angle precision caused by the artificial feeding to ensure the whole plate surface of the flatness accuracy is within 1 mm. In addition, make sure there is an uniform air film and belt running smoothly.
5. Welding robot: the plenum chamber adopts two sets of FANUC welding robots with laser positioning and automatic location in synergism. The precision of special welding is within 0.5 mm, and all the supports of the air supported belt conveyor are welded by another two sets of FANUC special welding robot.
6. Muti-functional shot blasting machine: the new shot blasting machine put into use not only can realize the whole surface of processing, but also the surface treatment can be carried out for all-around shot blasting under the condition of no turning over of workpiece without dead angle. The effect of removing rust and work efficiency is greatly improved.