China began to develop in the mid-1980s, and it has been widely used in the construction of the modern national reserve in the 20th century. Therefore, the problems that occur in the actual use of the device are also more concentrated, such as the head of dust spills, tail dust spills, belt grain, belt deviation and so on.This article write the solutions of the problems.
1. Improvement of Dust Leakage at Head of Air supported Belt Conveyor
Air supported belt conveyors (hereinafter referred to as air-cushioning machines, the air-cushioning machines referred to in this article are all single-chamber air-cushioning machines). When the return belt passes through the drum section at the head, a large amount of dust will be generated. After the belt has driven the roller of the head to drive the roller, the surface is still dusty. Some of the dust falls to A and will accumulate over time. With the movement of the belt, part of the dust at A was taken away. After passing through the redirection drum, the belt was deformed and the dust adhered on the surface fell off, causing dust to fly around.
The improved measure is to add a hopper with a manual gate between the head drive roller and the roller. During the production process, when the dust is accumulated on the A site, the gate is opened and the dust is placed in the bag. Each shift can be operated once. In addition, an air suction port is provided on the side (the suction port is generally incorporated into the wind screen at the air blower throw cover).
There are several advantages to this improvement:
(1) Collecting the dust after it is collected can reduce its concentration in the air and effectively prevent the occurrence of dust explosion accidents; at the same time, it also improves the working environment and ensures the physical and mental health of on-site workers.
(2) Reduce labor intensity of cleaning and improve work efficiency.
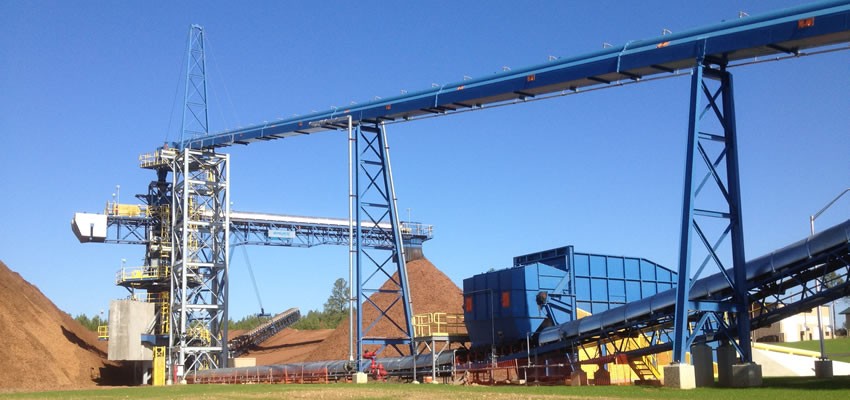
2. Improvement of Dust Leakage at the End of Air Supported Belt Conveyor
The air cushion machine under the silo, when close to the tail silo for warehouse operations, the air cushion machine tail (where there is generally no suction outlet, if you add the suction outlet due to the horizontal duct too long will result in clogging of the pipe dust, dust effect Often not ideal) Dust is often spilled. Therefore, we can consider a plug-in dust collector at the end of the air cushioning machine (the model selection is mainly based on the air transport volume, length and installation space).
The actual situation proves that installing the dust collector near the tail is better than in the middle. If the dust collector is installed in the middle, because there is not enough space to install the settling ash tank, the intelligence of the cleaned dust will directly return to the air cushion machine, and the pulse back blowing will still cause some dust overflow from the tail of the air cushion machine. The tail space is large, and an insert type dust collector with a settling ash box (a box made of channel galvanized steel sheet and a drawer made of a galvanized sheet at the bottom of the box) can be installed to effectively prevent the pulse injection bag from being ashy. Overflow, the effect is good.
3. The rectification of loose grains from the belt
When the air supported belt conveyor is running, there is often grain spillage on the return belt between the head reversing drum and the tail V-shaped cleaner, which may be due to the unreasonable design of the feed inlet. In addition, the air blower may be improperly selected, and the air pressure and air volume may be too small. Once this happens, the air cushion may not be fully loaded and may not even reach the rated delivery volume. If the working pressure and air volume of the fan meet the requirements, and grain cannot enter the air cushion between the belt and the air pan groove, the rated delivery volume of the air cushioning machine and the operating parameters of the fan can be determined first, and then the replacement of a suitable type of fan is determined.
4.The rectification of the guide plate at the inlet.
Air supported belt conveyors often block material during the transportation of domestic corn, affecting production, mainly because domestic corn is mixed with a lot of hemp rope, and often hangs on the guide plate under the feed inlet. The center part of the guide plate is cut into a trapezoidal shape, which not only ensures the function of the guide material, but also solves the problem of hanging grain by hanging the rope.
5.Improvement measures for belt deviation
The air supported belt conveyor was operating normally with no load, and the belt was deflected during the load, resulting in the shutdown of the entire conveyor system. This happens when the direction in which the material enters the air-cushioning machine is not the same as the direction in which the air-cushioning machine is running, mainly because the length-to-width ratio of the feed port is not appropriate. theory
It is better to say that the proportion of length and breadth is bigger, but to combine the actual situation on the spot, the ratio of the new sand grain bank is 2.5:1. In addition, it depends on whether the angle of the guide plate is reasonable and the empirical data is about 45°. Only by satisfying these two conditions can it be ensured that when the material enters the air cushioning machine, the direction and speed of the belt are basically the same, and it falls in the center of the belt. In addition, in addition to the direction of the material passing around the guide plate, the other three directions are added with rubber baffles to prevent food from spilling out of the belt.
After the above measures are fully implemented, if they still cannot solve the problem of deviation, other remedial measures should be taken.
(1) Air supported belt conveyor with gravity tension. In order to facilitate the adjustment of the air cushion machine, it is recommended to install a screw tension at the tail of it.
(2) It has been proved by practice that the anti-deviation effect of the bottom leveling roller of the air cushioning machine is obviously inferior to that of the anti-biasing vertical roller. It is recommended to use the anti-displacement roller instead of the leveling roller.
(3) The deviation sensor is generally installed on both sides of the return belt near the head or the tail drum. The JB standard does not specify the installation position of the deviation sensor. The manufacturer generally recommends that the horizontal installation distance of a pair of deviation sensors is equal to 1.06 to 1.1 times the belt width. Practice has proved that, under the principle of no belt tearing and other accidents, the horizontal mounting distance of the sensor can be as large as possible to ensure the stability of the system.
After all, the air supported belt conveyor is a new type of equipment, design and manufacturing is still not mature enough, but also in the practice of continuous improvement. It has many advantages than the flat conveying equipment.