The French client is a well-established energy and resource development company with operations in coal mining, mineral processing and related energy supply chain services. The company operates a number of open-pit coal mining projects in the south of France, and has long been committed to improving the automation level and production efficiency of the mines.
With the advancement of the equipment renewal plan, they put forward higher requirements for high-performance mining crushing equipment. At the end of last year, the customer contacted our company and asked for the Mineral Sizer for upgrading the raw coal crushing system of the coal mines.
The Mineral Sizer ordered by this French customer is tailor-made for its subsidiary coal mine project after our professional team fully understands the customer's actual needs and the working conditions on site. The Mineral Sizer ordered by the French customer is a tailor-made model for the subordinate coal mine project after our professional team fully understands the actual needs and site conditions of the customer, and finalizes the purchasing plan after several months of technical communication, program optimization and contract negotiation.
At present, the equipment has passed strict in-plant debugging and quality testing, successfully completed the packaging and loading on schedule, and was formally shipped to France today.
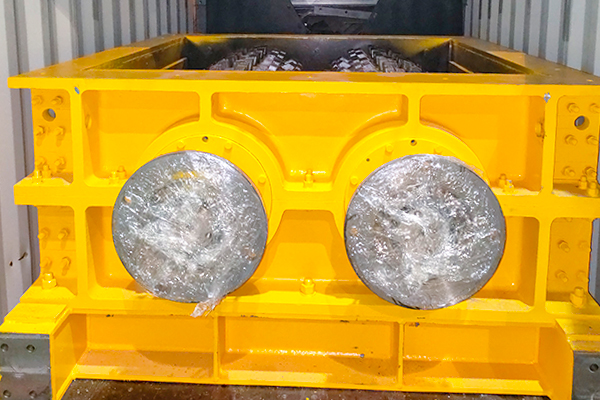
Toothed Roll Design
Advantage
Mineral sizer is a new type of crushing equipment, in addition to the obvious advantages of less pulverized coal output, simple structure, low power consumption, easy maintenance, high crushing capacity and durability, the most prominent advantage is: selective crushing of incoming materials of different particle size composition.
<Feature
The rotating rollers are like rotating sieves, materials meeting the size requirements can pass through directly, materials larger than the required size will be crushed, and all the products will meet the size requirements. Different tooth shapes and arrangements can be matched for different size requirements, so there is no need for closed-circuit process of screening and crushing, and then returning to crushing of the screened materials, and the qualified size can be obtained directly through the grading crusher.
Crushing + Screening
Mineral sizer plays the dual role of crushing and screening, which can simplify the crushing and screening system and reduce construction and equipment investment costs. The design of mineral sizer, in addition to the reasonable structure of the machine, crushing method is appropriate, the key also depends on the geometry of the crushing teeth and the arrangement of the form. Reasonable design and proper arrangement of crushing teeth can ensure the product size, optimize the composition of particle size, reduce over-crushing, save materials, extend the service life of the teeth, and reduce the crushing power consumption of the crusher.
Structure
The crushing tooth roller includes a roller shaft and a tooth ring set on the roller shaft, and the tooth ring includes a large tooth ring and a small tooth ring, and the large tooth ring and the small tooth ring are alternately set on the roller shaft, and this structural design can well grip and tear the material, play the role of two rolls and multi-stage crushing, and increase the area of the material passing through, so as to increase the production capacity of the equipment, and it has a very good practicability.
Tooth structure
Core requirements for tooth profile structure
The tooth structure of the crushing teeth should meet the following requirements: to meet the requirements of particle size under the premise of producing large particle size products, minimize over-crushing.
Overall Dimension
The external dimensions of the teeth, including tooth height, tooth width. Requirements are equal to or slightly smaller than the particle size of the product. The width of the root of the tooth is roughly 4/5 times the height of the tooth, the thickness of the tooth (i.e., the size of the tooth along the circumference) according to the strength of the crushed material, generally equal to or slightly greater than the height of the tooth. Under the premise of ensuring the strength of the teeth, the size should be reduced as much as possible.
The influence of tooth profile dimensions
If the tooth size is too large, the product size will be over the limit, losing the grading effect, and also affecting the passing capacity of the crusher. The tooth shape is too small, not only will make the strength of the teeth reduced, but also will make the phenomenon of over-crushing intensified, but also not easy to engage in the material.
The influence of material properties
The hardness and toughness of the crushed material also directly affect the particle size of the product, for materials with high toughness, the size of the crushing teeth and the size of the crushing space should be reduced accordingly. For example, when crushing coke, because of its high toughness, the crushing space should be equal to or greater than the required crushing size. For coal, because of its lower toughness and higher brittleness, the crushing space should be slightly larger. At the same time, the toughness and brittleness of different coals are also very different, and should be determined for different situations. For materials with high hardness, in addition to the corresponding reduction of crushing space, the width of the root of the teeth should be relatively increased to improve the strength of the crushing teeth.
The significance of stress distribution on broken teeth
When the crushing operation is carried out, the stress distribution of each part of the crushing teeth is even, which can improve the service life of the teeth and the efficiency of the material use, and save the material; secondly, the weight of the crusher can be reduced, which can minimize the useless work and reduce the power consumption.
The form of wear of teeth
Breaking Principle I
Mineral sizer, which is completely different from the traditional crusher to rely on impact and extrusion to break the material, but use the joint action of shear and stretch to achieve material crushing, it adopts a blend of high torque, low roll speed and truncated tooth shape to get a specific product size, and make the over-crushing to reach the minimum of a kind of advanced crushing technology.
It is characterized by high crushing strength, large processing capacity, adjustable particle size rigidity, less super-granule and over-crushing, capable of handling sticky and wet materials, and good environmental protection performance, etc. It is equipped with an automatic control system, which can be conveniently incorporated into the centralized control of the whole plant. It is mainly used in coal, electric power, mining, metallurgy, chemical industry and other industries in the hard materials below the crushing.
Breaking Principle II
Its main working parts are two parallel mounted crushing rolls, each crushing roll along the axial arrangement of a certain number of crushing teeth (tooth plate), according to the nature of the crushed material and the parameters of the different inward and outward rotation, the material is either pulled apart under the mutual perpendicular stress, or the effect of shear force to produce slippage, or in the joint action of both broken.
It mainly realizes the purpose of crushing through the action of shearing, piercing and splitting of materials, and makes full use of the strength characteristics of most rock and mineral materials such as rock, coal, coke, etc.: compressive strength > shear strength > tensile strength.
At the same time, mineral sizer's crushing tooth type and its arrangement form according to the actual requirements and special design, large materials are engaged in a one-time, less than the required particle size of the incoming material will be directly through the crushing chamber without being crushed twice. In addition, the rotational speed of the grading crusher is very low, which reduces the chance of scraping the material by the crushing teeth during the crushing process, and directly reduces the content of pulverized coal in the product.
Wear of the teeth
The above crushing mechanism not only improves the processing capacity of the equipment, reduces over-crushing and saves crushing energy, but also there is no violent impact and impact on the material in the crushing process, which not only causes less loss of the block rate, but also reduces the hidden fissures and residual stress in the crushed material, which reduces the chances of secondary crushing in the subsequent storage and transportation and processing process, and thus guarantees the block rate of the products in an all-round way. The rate of product lumps is guaranteed in all aspects.
From the working principle of the mineral sizer and the field application situation, it can be seen that the wear of the crushing teeth is mainly based on the position of abrasive wear, accompanied by a certain degree of impact.