Introduce
In the field of ore crushing, mineral sizer is the core equipment to improve crushing efficiency and ensure the crushing quality, it can effectively separate and crush ore with different particle sizes, laying a solid foundation for the subsequent processing process, and Synchromesh Gear plays a key role in ensuring the crushing efficiency and operational stability of the equipment.
Synchromesh Gear is the core part of primary mineral sizer design, and its performance directly affects the working performance of the equipment: if the gear synchronization accuracy is high, the equipment crushing uniformity is good and the efficiency is high; on the contrary, it will lead to poor crushing effect and increased energy consumption.
At the same time, it also relates to the life of the equipment, high-quality Synchromesh Gear can reduce the wear and tear of the components, to extend the life cycle of the equipment; and its operating status will affect the maintenance frequency and cost, which in turn affects the overall operating costs.
Working Principle
Synchromesh Gear is installed at the end of the rolls of the mineral sizer, which builds up a stable transmission relationship through the precise connection with the main shaft and the sub-shaft. When the equipment is in operation, Synchromesh Gear will drive the main shaft and sub-shaft to rotate in synchronization according to the set transmission ratio, so as to ensure the synchronous movement between the rollers and avoid uneven crushing or jamming of materials due to the inconsistent speed of the rollers.
In addition, the tooth shape design and meshing accuracy of Synchromesh Gear are precisely calculated to ensure the stability of gear meshing during the rotation process. This stable meshing relationship makes the force of the rollers on the material uniform and continuous, which ensures even crushing and smooth discharging of the material, providing a basic guarantee for the efficient operation of the equipment.
Materials and Wear Resistance
Synchromesh Gear is commonly made of high alloy steel or wear resistant alloy steel. These materials have a high degree of hardness, strength and wear resistance, and can withstand the harsh conditions that mineral sizers are subjected to when crushing ores.
In the mineral sizer high load working environment, Synchromesh Gear need to withstand huge impact and friction, and high alloy steel or wear-resistant alloy steel Synchromesh Gear, with excellent wear resistance, can effectively resist the wear and tear of the material crushing process, to reduce the wear and tear of the gear tooth surface.
The choice of material has a significant impact on gear life and efficiency. High-quality wear-resistant materials can extend the service life of gears and reduce the number of downtimes caused by gear wear and replacement; at the same time, the stable performance of the material can ensure that the gears maintain good meshing accuracy in long-term use, avoiding the deterioration of the material leading to a decline in transmission efficiency, thus ensuring the working efficiency of the equipment.
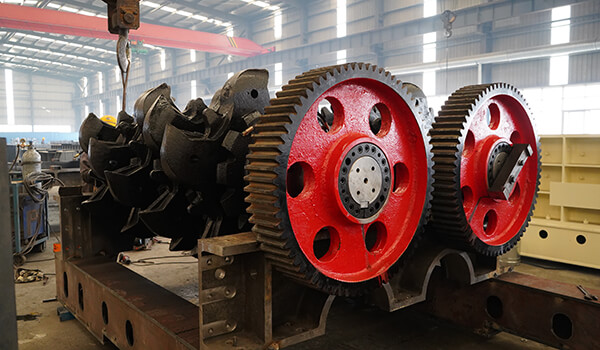
Load bearing capacity
mineral sizer When crushing large, hard ores, the Synchromesh Gear is exposed to extreme loads. These loads include not only the pressure from the weight of the material itself, but also the impact and torque generated during the crushing process.
Synchromesh Gear has a strong load bearing capacity, its design through the optimization of the gear structure and material strength, can bear the load evenly distributed to each tooth and shaft system, to avoid excessive local force and lead to excessive wear or failure, to ensure that the transmission is still stable under high load conditions.
High-load performance
When mineral sizers process harder materials, Synchromesh Gear needs to withstand greater impact and torque. In this case, a high-quality Synchromesh Gear, with good material properties and structural design, is able to transmit power stably and ensure the synchronized operation of the rollers.
Under high loads, Synchromesh Gear avoids damage problems such as stalling and tooth breakage due to excessive force by precise meshing relationship and sufficient strength. It transmits power to the rolls smoothly, ensuring continuous crushing of hard materials and maintaining the normal working rhythm of the equipment.
Advantages of Synchromesh Gear
Compared with traditional gears (e.g. spur gears, helical gears, etc.), Synchromesh Gear has many advantages. Traditional gears are prone to poor gear meshing during operation, while Synchromesh Gear is designed to pay more attention to meshing precision, which can effectively avoid this problem;
at the same time, Synchromesh Gear has less noise and vibration during transmission, which is due to its smoother meshing, reducing impact and friction between gears; in addition, Synchromesh Gear has a higher transmission efficiency, which can improve the working efficiency of the equipment. In addition, Synchromesh Gear has a higher transmission efficiency, which improves the working efficiency and operational stability of the equipment.
Synchromesh Gear in mineral sizer
Transmission Synchronization
Synchromesh Gear ensures precise synchronization between the main shaft and the secondary shaft, keeping the rotational speeds and rotational phases of the two in line and avoiding poorly meshed or out-of-sync gears. This reduces abnormal friction and collision between the gears and reduces gear wear.
Improved crushing efficiency
Synchromesh Gear allows the rotation of the toothed rolls, the feeding of the feed unit, and the unloading of the discharge unit to be coordinated and synchronized in rhythm by coordinating the movement between the different gears. This ensures that the feeding, crushing and discharging processes of the mineral sizer are smoothly integrated and reduces the time the material is left in the machine, thus increasing the overall crushing efficiency.
Reduced Noise and Vibration
The precision-designed Synchromesh Gear operates with an even mesh gap between the gears, resulting in a smooth transmission that reduces the noise generated by gear collision and friction. At the same time, the smooth transmission also reduces the vibration amplitude of the equipment, ensuring the stability of the equipment, reducing the damage of vibration to the various components of the equipment, and prolonging the service life.
Reduced Energy Consumption
Synchromesh Gear optimizes the gear tooth shape and meshing angle, which reduces the energy loss of gears during transmission. Efficient transmission allows more energy output from the motor to be converted into effective work of crushing materials, reducing energy loss and thus lowering operating costs.
Extended equipment life
Through precise synchronized operation, the components within the equipment fit together more harmoniously, avoiding additional stress and abnormal wear caused by unsynchronized movements. This reduces the probability of damage to the components, which in turn extends the service life of the mineral sizer.
Efficiency of Synchromesh Gear
Synchromesh Gear plays an important role in improving the efficiency of mineral sizer. It ensures that the rolls and other components operate at an optimal rhythm through precise transmission, avoiding problems such as material buildup and untimely crushing caused by lagging or turbulent transmission.
At the same time, the Synchromesh Gear ensures efficient operation between gears and reduces wasted energy due to poor gear meshing. Every bit of energy input can be more effectively applied to material crushing, thus improving the overall working efficiency of the machine.
Stable Operation at High RPM
The Synchromesh Gear is designed with optimized tooth shape and structure to maintain good dynamic balance at high RPM, reducing vibration and deflection caused by excessive centrifugal force. In addition, the lubrication system provides adequate lubrication to the gear mesh at high speeds, reducing the heat generated by friction and preventing the gears from overheating.
It is the synergy of this design and the lubrication system that allows the Synchromesh Gear to operate efficiently and stably at high speeds, preventing overheating, wear and tear, or other failures caused by excessive speed.
Common Failures
Common failures of Synchromesh Gear include gear wear, poor gear mesh, and excessive slippage. Gear wear is mostly caused by prolonged exposure to friction and impact, or insufficient lubrication; poor gear meshing may be caused by insufficient mounting accuracy, wear and deformation of gear teeth; and excessive slippage may be related to excessive loads and insufficient friction between gears.
In order to prevent these failures, it is necessary to carry out regular maintenance: regularly check the wear of the gears, add or replace the lubricant in time; for the gears with serious wear and deformation of the tooth shape, replace the wearing parts in time; at the same time, ensure the installation accuracy to ensure that the gears mesh well. Through these measures, the reliability of the equipment can be improved.
Conclusion
Synchromesh Gear has a vital role in mineral sizer, which is directly related to the crushing efficiency, operational stability, service life and energy efficiency of the equipment. High-quality Synchromesh Gear can significantly improve equipment performance and reduce operating costs.
Therefore, ensuring the quality and performance of Synchromesh Gear is one of the key considerations when choosing a mineral sizer. Only a reliable Synchromesh Gear will ensure that the mineral sizer will perform optimally in ore crushing operations.