Introduce
With the increase in demand for minerals and the decrease in high-grade ores, coal mines often need to deal with hard materials containing clay and other impurities, and traditional crushers are susceptible to problems such as clay clogging.
The mineral sizer has significant advantages. It combines screening and crushing functions in one, and can be operated separately to simplify the process. The spiral arrangement of crushing teeth sieves qualified materials like a grating screen and only crushes the over-standard part, resulting in high block rate, low over-crushing rate and low energy consumption.
Its double-tooth roll drive structure is simple, smooth running, low vibration, low noise, less dust, suitable for coal mine environment. The size of the toothed roll is optimized according to the demand, and the particle size is precisely controlled. The crushing teeth are made of high-strength alloy with wear-resistant surfacing, and the rolls are hardened for durability and easy maintenance.
It can also adjust the roll pitch through the eccentric bearing cup to meet different needs; it has self-cleaning mechanism to cope with sticky and wet materials, and overload protection to ensure safety, which is especially suitable for the complex working conditions in coal mines, so it becomes the first choice.
Working Principle
The action of the crushing teeth on the material process can be divided into three stages.
First Stage
The first stage is when all the granularity of the material is fed into the crusher, less than the size of the material along the teeth before the space and the teeth of the side gap and the gap between the tooth rolls and the side of the comb plate through the crushing rolls directly discharged, such as rotating roller sieve like to achieve the purpose of grading, and at the same time will be the two sides of the crushing rolls and the comb plate between the larger than the size of the required material roll into the two crushing chamber for the next step in the crushing.
At the same time, the material larger than the required size between the two sides of the crushing rolls and the comb plate will be rolled into the crushing chamber between the two crushing rolls for the next crushing.
Second Stage
The second stage is the teeth of the material larger than the size requirements of stabbing, shearing, tearing and other crushing, in this section, the movement of the teeth suddenly encountered large pieces of material, relying on the staggered tooth tip of the first material for stabbing and shearing, if the large pieces of material is not broken then further tearing.
After crushing the material that is engaged by the teeth, and the third section of the crushing. If the material is still not crushed, the teeth along the surface of the material is forced to slide through, by the teeth of the spiral arrangement, the material will be turned over, waiting for the next pair of teeth to continue to play a role until the crushing to the material can be engaged until.
Third Stage
After the second stage of crushing, the material has been initially crushed to the particle size can be engaged by the rollers, so as to enter the third stage of crushing. In the third section mainly rely on the former pair of teeth of the front tough and the opposite pair of teeth of the back tough shear, extrusion and crushing materials, this crushing section from the material is meshed into the beginning, to the former pair of teeth out of the meshing termination.
The performance of a pair of teeth included in the cross-section from large to the smallest process, this process is the process of crushing and discharging materials, particle size of the material due to the inclusion of the volume gradually becomes smaller and was forced to squeeze the broken, broken material is extruded from the teeth side gap leakage.
When the former pair of teeth began to disengage from the meshing, the cross-sectional area contained between the teeth began to gradually increase from the smallest, by the third section of the crushed material, accompanied by the separation of the two pairs of teeth and under the leakage of discharge.
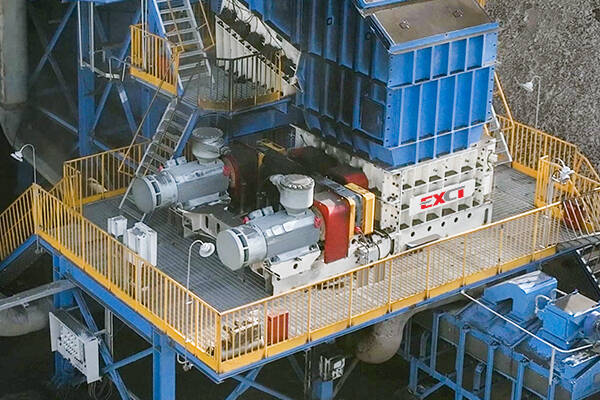
Performance characteristics
Screening + Crushing
mineral sizer integrates the dual functions of screening and crushing, which makes it possible to complete screening and crushing operations independently without relying on other auxiliary equipment.
Whether it is screening the material first, separating the part that meets the particle size requirements, and then crushing the material exceeding the standard, or in the crushing process to achieve the effect of simultaneous screening, can be efficiently completed, greatly simplifying the production process, reducing the equipment footprint and investment costs.
Crushing teeth
The crushing teeth adopt scientific spiral arrangement, when the two rolls rotate relative to each other, the space formed by them is like a precise grating screen. This design can accurately screen out materials smaller than the product size, so that it passes through directly, only for materials larger than the product size requirements for targeted crushing.
This process fundamentally avoids the defects of mixed crushing of coarse and fine materials in traditional crushing equipment, which not only greatly improves the block rate of the crushed products and ensures the integrity of the materials, but also significantly reduces the over-crushing rate and reduces unnecessary material loss, and at the same time, reduces the energy consumption in the crushing process, realizing the energy-efficient operation effect.
Drive
adopts the drive mode of “motor + hydraulic coupler + reducer”, which has a simple and compact structure and high transmission efficiency. During operation, the equipment has strong stability and low vibration amplitude, which effectively reduces the wear and tear of the equipment and the impact on the surrounding environment caused by vibration.
At the same time, the operation of the noise is lower, less dust emissions, for the operator to create a more comfortable, more environmentally friendly working environment, in line with the requirements of modern industrial production on the green environment.
Toothed rolls
The structural dimensions of the toothed rolls are not set in stone, but are precisely optimized according to the particle size of the required product. Through this customized design, the equipment is able to forcibly crush the materials, strictly control the geometric size of the space through which the materials pass.
And ensure that the particle size of the crushed materials is uniform and consistent, which is fully in line with the requirements of the production process, avoiding the problems of the subsequent processes due to the unqualified particle size.
Self-cleaning device
In order to cope with the crushing problem of sticky and wet materials, the equipment is specially equipped with a self-cleaning mechanism. When crushing sticky and wet materials, the self-cleaning mechanism can timely remove the materials attached to the rolls and the inner wall of the equipment.
Preventing the materials from sticking, caking and clogging, ensuring the normal operation of the equipment, effectively expanding the scope of application of the equipment, so that it still performs well when dealing with high humidity and high viscous materials.
Overload protection
The equipment is also equipped with a reliable overload protection device. When the equipment encounters too much material, too hard or other unexpected circumstances during operation that cause the load to exceed the rated value, the overload protection device will respond quickly to cut off the power or issue an alarm in time to avoid damage to the equipment due to overload.
Thus guaranteeing the safe and reliable operation of the equipment and the whole production system, reducing the risk of production accidents, and providing a strong guarantee for continuous and stable production.
Features
Grooved Hubs Grooved hubs made from high strength cast alloy steel provide long term stability and reliability of the rolls in demanding crushing applications.
The modular housing design facilitates quick and easy maintenance of the rolls to accurately control the size of the product while generating very little dust and oversize product.
Designed for maximum output, the rolls - the heart of the crusher - provide excellent performance in crushing a wide range of materials that are wet, dry, hot, cold, sticky, hard and abrasive.
New material crushing teeth, high strength, wear-resistant, large capacity, high reliability, low noise, less dust. The one-time life is not less than 15000h, and can be surfaced or replaced on site after grinding.
No screen grate bottom, no requirement for the moisture content of the material, there is no problem of paste plugging the screen plate, not to mention the problem that fine powder can not be discharged in time and repeated crushing.
Closed gear box so that the two rollers to achieve complete positive meshing.
Sticky and wet materials do not stick, no clogging, self-cleaning.
Centralized lubrication system can provide semi-automatic or full-automatic lubrication system.
Fluid coupling, flexible transmission, self-adaptation, shock mitigation, vibration isolation, light load start, overload protection.
Reducer, after deceleration the speed of the rollers is reduced, torque is greatly increased, forming a strong crushing, especially for hard materials such as stone.
PLC sequence control of electric control system can adapt to the harsh environment. Generally adopts explosion-proof motor, multiple safety protection for moving parts. The control cabinet adopts double-layer stainless steel shell, fully sealed structure, waterproof and dustproof.
Materials handled
Coal
In the field of coal processing, the mineral sizer shows great adaptability, and can efficiently handle different kinds of coals from raw coal to refined coal after sorting and processing, including lignite, which is soft and has high moisture, bituminous coal, which has obvious smoke flavor and adhesion, sub-bituminous coal, which is between bituminous coal and anthracite, and anthracite, which has high ignition point and is smokeless when it is burned. anthracite, and frozen coal which is frozen in low temperature environment and difficult to handle, to ensure that all kinds of coal can reach the ideal particle size requirements in the subsequent utilization.
Coal gangue
The mineral sizer can also easily deal with the gangue, which is the hard roof and surrounding rock that coexists and accompanies with coal seams, as well as the gangue that is screened out in the process of coal processing. These materials are often high hardness and complex composition, but it has a certain use value in the field of resource recovery, filling, etc. Through the treatment of this equipment, it can realize the reuse of resources.
Coke
In coke processing, whether it is petroleum coke used for industrial fuel, metallurgical coke indispensable to the metallurgical industry, or raw petroleum coke that has not been fully calcined and roasted coke after roasting treatment, the mineral sizer can be crushed accurately according to the physical characteristics of different coke, to meet the subsequent production of the strict standards for its particle size.
Fertilizers
In the field of fertilizers and potash, materials such as MAP (Mono Ammonium Phosphate), DAP (Diammonium Phosphate), natural potash ores and processed potash flakes are different in nature, with some being prone to humidity-absorbing agglomerations and others being hard. mineral sizer can properly handle these materials to ensure that they are in good condition during storage, transportation and use.
Limestone
For quicklime and limestone, whether it is limestone and dolomite with a texture ranging from soft to medium hardness, used as adsorbents in boilers, calcined quicklime or slaked lime produced by reacting with water, the equipment is able to efficiently process them, guaranteeing their application in the fields of environmental protection, construction and so on.
Ore
Soft ores such as shale, clay, phosphate, oil shale, etc., usually have the characteristics of laminar structure or softer texture. mineral sizer can carry out moderate crushing according to its characteristics, which not only ensures the crushing efficiency, but also reduces the wear and tear on the equipment.