Dry mix mortar production line is a dry-screened aggregate (such as sand) , Gelling materials (such as cement, coal ash), chemical additives, etc. through measurement control, reasonable proportion, mixing homogeneity, mechanized production, product packaging or bulk storage and transportation to the site, as long as the work is done by adding a certain proportion of water and mixing, it can be directly used.
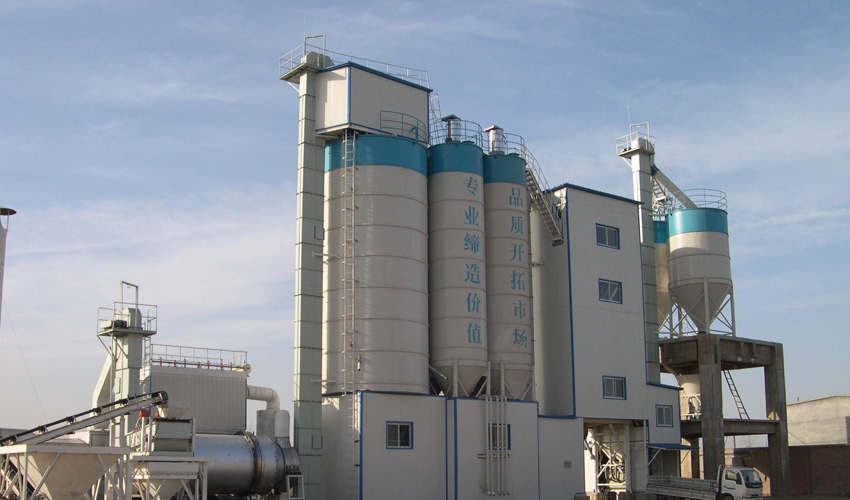
1. Accurate batching measurement system
There are many ways to measure, of which the best performance and most used is the improved screw conveyor. It is suitable for almost all powdery materials. It has the following advantages: adjustable range, high measurement accuracy, wear resistance, simple maintenance and low operating costs.
2. Lifting conveyor equipment
Screw conveyors, bucket elevators: In view of the high failure rate of screw conveyors, bucket elevators are still choose by most manufacturers. The power is determined according to the lifting height and material specific gravity; the head wheel is covered with rubber to prevent the belt from slipping. A dust collecting cover and grating are arranged above the hopper to absorb dust and prevent large foreign matter from entering the mixer.
3.Efficient mixing system
In
dry mix mortar prodution line, high efficiency mixer should be: high mixing uniformity, high mixing efficiency, fast unloading speed, and it should be completed within 10 to 40 seconds; No residual unloading, generally do not need to clean the mixing machine; Low energy consumption. Equipped with high-speed blades; overall wear resistance design.
4.Silo system
In order to improve production efficiency, the preparation of the silo is mounted above the mixer, so that there is always a batch of the prepared materials waiting for mixing, which can increase the production efficiency by 30%. Secondly, the material will form a gas arch and it is difficult to discharge, thus the silo should be equipped with a gas-assisted air cushion or a vibration motor. For maintenance and sealing, the silo port should be equipped with a pneumatic or manual valve; in order to smooth the material. The cone angle of the silo should not be greater than 60 degrees. When the valve of the admixture hopper is opened, dust will fly out, so the dust collection port should be added to the small hopper.
5 .Valve pocket packaging machine
Valve pocket packaging machine: Equipped with mechanical broken arch device, it solves the problem of material bridging; the device is completely sealed, and the dust collecting port is installed at the discharge port to prevent dust from flying; Electromechanical integration, saving energy, the machine can automatically achieve the compression, loosening, closing of the shutter and off the bag.
6. Dust removal system
Dust collection is an important means to improve the on-site working environment of
dry mix mortar production line. It should be dust collected when sending the powder and the mixture with the powder enter the mixer. Therefore, the dust collection system must be installed in the whole equipment.
7. Gas balance system
The pipeline (PVC) is used to connect the preparation silo, the mixer and the finished product warehouse, and a venting cap is mounted to the mixer and the upper silo, to balance the atmospheric pressure with the outside world, reduce dust and increase mixing uniformity.
Owing to errors and chaotic ratio exist in the mixing of the mortar at the construction site, the optimization of the raw materials cannot be achieved.
dry mix mortar production line is an industrialized product, which is not only accurate in measurement, but also all the mixing ratios are obtained through optimized design and adaptation. On the other hand, the
dry mix mortar production line can pre-treat various raw materials. The use of water-retaining and thickening materials is a significant improvement in the operability, caking ability and durability of dry mix mortar. Under the existing construction conditions and technology, the construction quality of masonry and stucco can be greatly improved, and the current prevailing problems such as seepage, leakage and cracking provide effective guarantee for the quality of the
dry mix mortar product.